In the fast-paced world of machining, speed is of the essence. However, quality parts are just as important. So, what’s the key to marrying quality and efficiency? Lean manufacturing. A strategy designed to continuously optimize the manufacturing process through the elimination of waste, lean manufacturing is the smart solution to improve manufacturing operations while reducing production costs. To better understand how this works, let’s look at some of the lean manufacturing techniques and how they streamline the manufacturing process.
Stay Ahead of Supply Chain Issues with Our Helpful Infographic!
Optimizing Through 7 Lean Manufacturing Techniques
1. Kaizen
Embodying one of the fundamental principles of lean manufacturing, Kaizen is the concept of working towards continuous improvement. This technique is done through philosophy (the mindset of improvement) and action—like the quality control process we have at Winndeavor to ensure we’re always evolving for the better. Kaizen proactively targets small improvements that add up to an overall more efficient manufacturing process.
2. Error Proofing
Error proofing is the lean manufacturing technique of intentionally designing preventative measures into the production process to eliminate the chance of defects. This tactic identifies issues as they occur, which stops defected pieces from moving down the production line, saving you money, time, and other resources.
3. 5S
Standing for sort, set in order, shine, standardize, and sustain, 5S reduces waste and time on a micro level through organizing everything from tool placement to shop floor layout. Shop managers tend to think of 5S very early on within production compared to other lean manufacturing techniques because it optimizes efficiency with a strategic machine shop layout, therefore promoting ideal workflow.
4. Just-In-Time
Production based on projected demand can lead to excessive inventory, thus wasted storage space, human resources, machine availability, time, and money. Just-In-Time solves this by pulling parts through production based on customer demand, which minimizes waste.
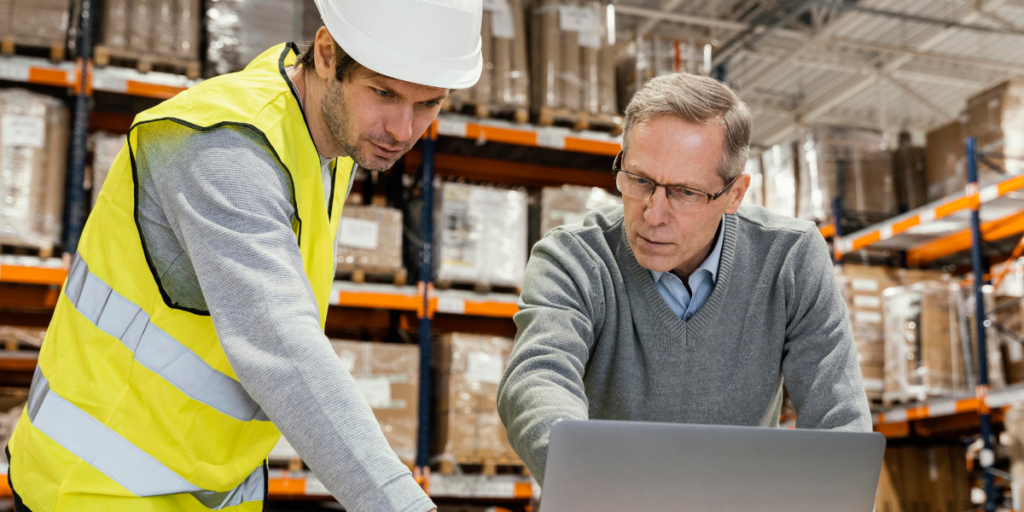
5. Bottleneck Analysis
A bottleneck is a point of congestion that stops or severely slows production, which can create delays and higher costs. To combat this roadblock, manufacturers use Bottleneck Analysis to identify the weakest link within the manufacturing process and what can be improved within it. Once these advancements are made, the bottleneck opens, allowing operations to run smoother and at lower cost.
6. Overall Equipment Effectiveness
Overall Equipment Effectiveness (OEE) allows you to measure the productivity loss for a manufacturing process. Tracking down time, slow cycles, and rejects, OEE provides the manufacturer with a baseline and a tool for tracking progress. Striving for a higher OEE percentage means better quality parts at a faster pace, with no downtime.
7. Machine Monitoring
Lean manufacturing techniques can often be combined to create a stronger lean strategy, such is the case with OEE and Machine Monitoring. Machine Monitoring is the automatic process of collecting data from production machines. Operators and management use this information to gain a better understanding of their OEE and make faster, more informed decisions.
Reaping the Benefits of Lean Manufacturing Techniques
On their own or combined with others, these lean manufacturing techniques are essential to how the lean strategy speeds up the manufacturing process, improves production quality, and reduces production costs. Ready to see these improvements and more within your own operations? Learn more about the advantages of lean manufacturing for your organization.
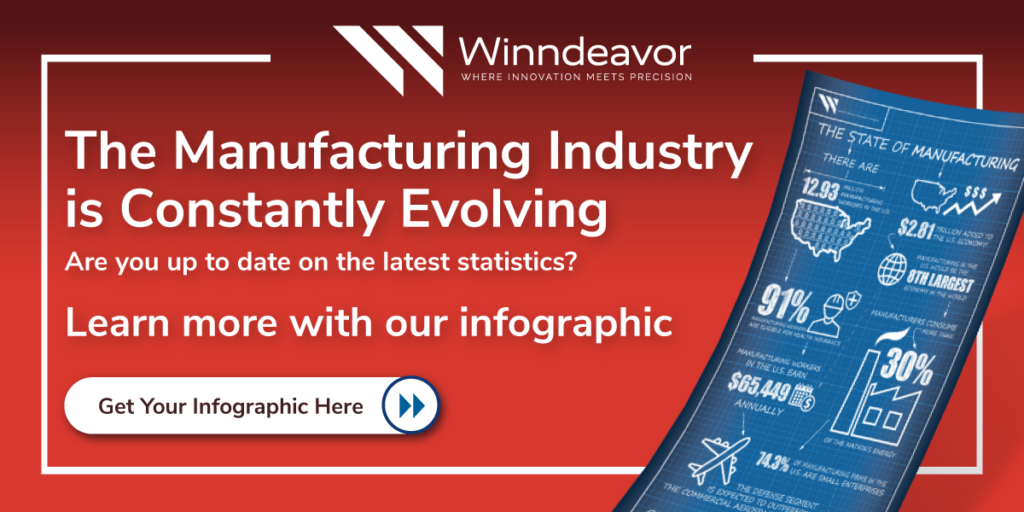