In today’s globally-connected marketplace, parts can be ordered anywhere in the world. The challenge for those ordering parts from new vendors in distant places is understanding the level of quality to expect from organizations they have never done business with.
Enter the ISO 9001 certification—indicating that a manufacturer or job shop implements a strict quality management system (QMS) based on international standards. In gaining this certification, a manufacturer goes through a process that does more than just establish a quality control system. An ISO 9001 certification indicates a rigorous process that includes assessing goals, structure, and how the company works as a whole.
Click Here to Learn About Setting Up Vendor-Managed Inventory
Here are a few aspects of an ISO 9001 certified manufacturer that ultimately will help you, as a customer, achieve your goal of reliably obtaining quality parts within a lower-cost structure.
1. ISO-certified shops are better decision-makers:
The process of becoming ISO 9001 certified requires us to evaluate all of our processes with the goal of improving quality and reducing waste. We must be able to provide quantifiable data for each process in order to monitor and gauge for constant improvement. This level of data allows us to make better decisions not only in our processes, but for the customer and their product as well.
2. We actively seek to reduce waste and improve efficiency:
The ISO 9001 certification requires us to have a QMS that focuses on preventative measures, allowing us to address any problems before they result in a large amount of defects and waste. This process pushes us to constantly improve our processes and be more efficient.
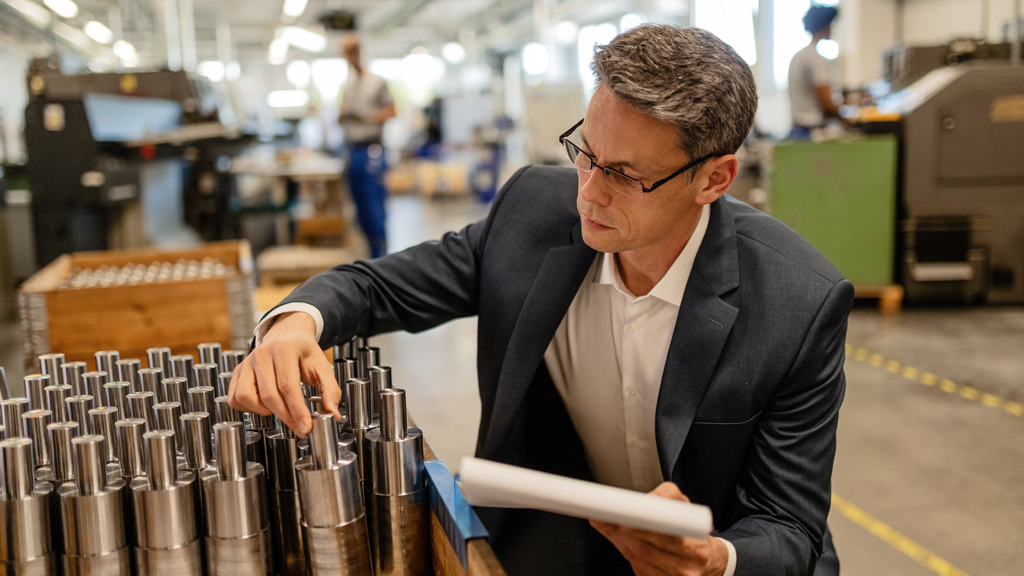
An engineer performing a visual inspection of parts as part of a QMS.
3. Increased staff knowledge and performance:
ISO 9001 requires us to maintain our QMS containing procedures, documents, responsibilities, and processes for quality processes and objectives. All employees are guided by this QMS and are required to adhere to it, engaging them in the process. In addition to the QMS, ISO 9001 requires continued training for employees to keep them up-to-date with technology and procedures.
4. We provide better customer service:
The ISO process is based on the needs of the customer, reliably providing quality parts, and reducing waste. The more dedicated we are to our QMS the more value we can bring to our customers.
An ISO 9001 certification isn’t just an acknowledgment that a manufacturer or job shop can produce parts of a certain quality. It is the overall result of a dedicated process to implement a QMS that focuses all the company’s processes and procedures on increasing efficiency and reducing waste which adds value to the customer.
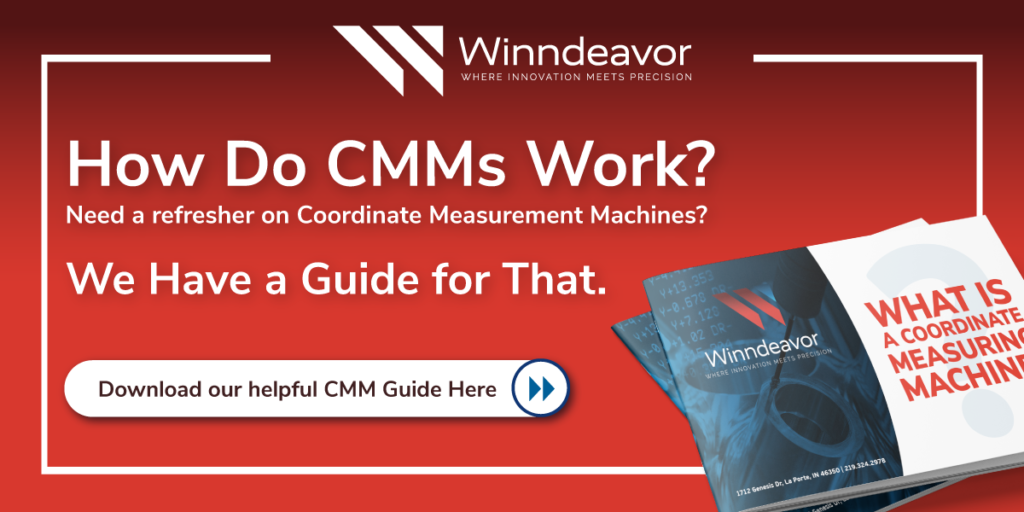