When we talk about different types of machining processes, we know that the unsung heroes of such processes are the machine tools used to craft the parts we use in everyday life. One of the key tools used for machining (and one of our favorites) is the lathe! CNC lathes are exceptionally versatile: just as every great baseball team needs a utility infielder, so too does every great machine shop need a lathe. Let’s explore the various tasks lathes can handle.
Find out How to Implement a VMI Strategy
Before we can even talk about the most common CNC lathe operations, we must first establish that lathes are capable of machining both the interior and the exterior of the part. Internal operations will work to modify the inner diameter of the workpiece, while external operations shape the exterior.
Now, let’s get into more detail.
Internal Operations
Drilling: In this process, a drill enters the workpiece axially through the end of the workpiece and cuts a hole with a diameter equal to that of the cutting tool.
Boring: A boring tool enters the workpiece axially and cuts along the internal surface to form different features like steps, tapers, and contours. The tool is a single-point cutting tool, which can be set to cut the desired diameter. Boring is often done after drilling to enlarge the diameter or to achieve more precise dimensions.
Reaming: Like boring, reaming is often done after drilling. The reamer will enter the workpiece axially and enlarge an existing hole. Reaming is meant to remove a minimal amount of material for a more accurate diameter and a smoother internal finish.
Tapping: In this process, the tap enters the workpiece and cuts internal threads into a previously drilled hole.
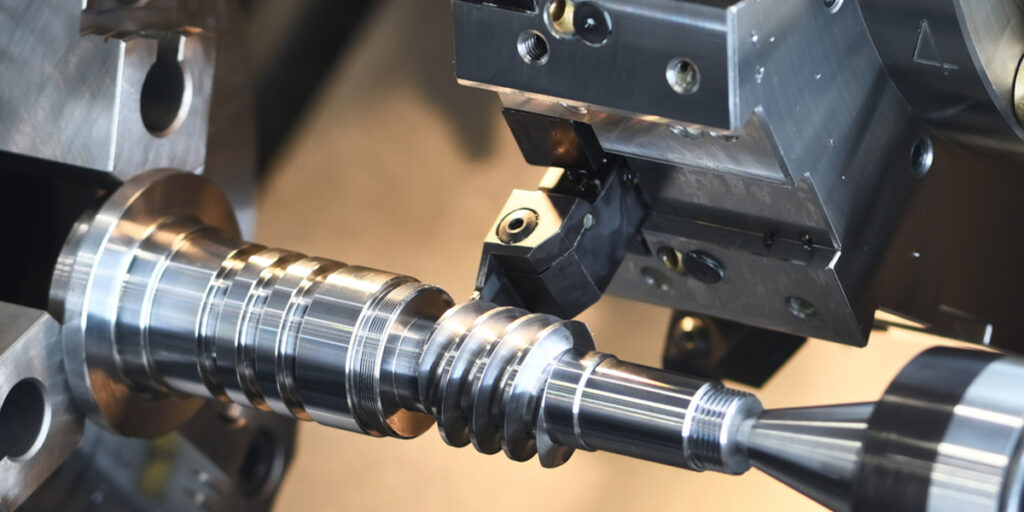
CNC Lathes are capable of completing many tasks, including threading.
External Operations
Turning: Turning is perhaps the most basic operation a lathe performs. In this process, a single-point cutting tool moves axially, along the side of the workpiece to remove material; this forms different exterior features such as steps, chamfers, and tapers. Such features are typically machined with many passes with small depth of cut until the needed diameter has been achieved.
Facing: In this process, a single-point tool moves radially along the end of the workpiece. This removes a thin layer of material to provide a smooth, flat surface. The depth of the face is very small, so facing can often be used as a precision finishing process.
Thread Cutting: If tapping is the method for threading the interior of the part, threading is the inverse. In this process, a single-point threading tool (usually with a 60-degree pointed nose) moves along the side of the workpiece to cut threads into the outer surface. The threads can be cut to a specified length and pitch and may require multiple passes to ensure the desired size or dimension.
Grooving and Cut-off: In grooving, a single-point cutting tool moves radially into the side of the workpiece to cut a groove equal to the width of the tool. When wider grooves or when grooves of various geometries are needed, multiple passes are made. The cut-off process is similar to the grooving process, but the tool continues to the center of the workpiece to cut the part from the stock.
In addition to these static tool operations, modern CNC lathes utilize live tools, which are driven by the turret. With a live tool, you can perform secondary operations such as drilling, tapping, or milling, both on the face of the part and around the diameter.
CNC lathes are the centerpiece of every great machine shop in part because of their unrivaled versatility and speed. The team at Winn Machine are skilled using lathes to make accurate, high-quality parts in a variety of quantities. If you have a project and you’d like to learn how lathe expertise can deliver optimal results, contact us today!
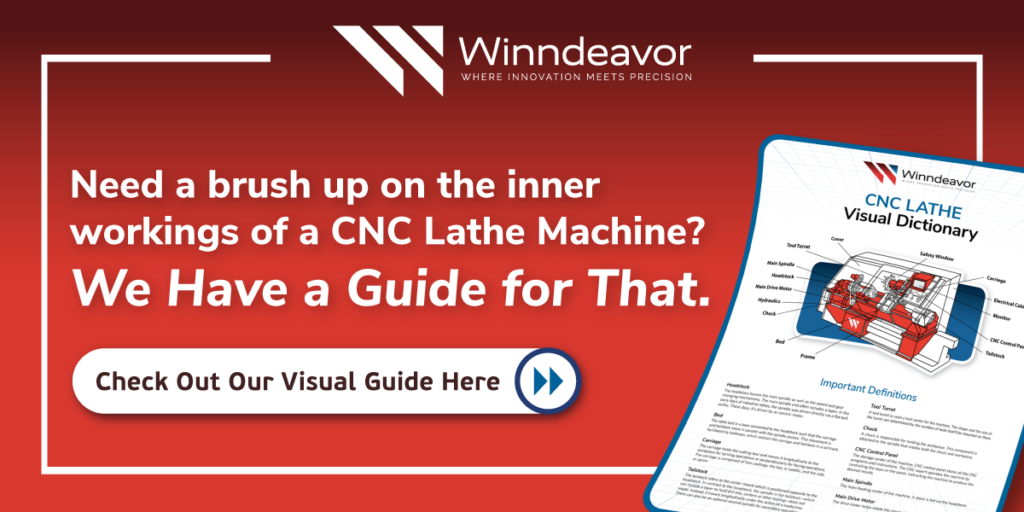