In recent years, developments in manufacturing have led to so many solutions that when manufacturers are identifying which is best for them, the sheer number of solutions can be immediately overwhelming. While these developments have led to increased efficiency, productivity, and therefore profitability, they have also introduced increased complexity into the buying process. Ultimately, though, there are only two primary types of manufacturing, which can be a much better starting point to the process. Let’s talk about additive manufacturing, and subtractive manufacturing, how they work, and when each should be used.
Find out How to Implement a VMI Strategy
Additive Manufacturing
Let’s start with additive manufacturing. Additive manufacturing describes the process of producing parts and products by adding layers of materials on top other layers to shape parts and products. Because of the definition of the process itself, additive manufacturing is frequently associated with 3D printing. This is because additive manufacturing begins with the creation of a 3D model through a computer-aided design (CAD) program. After designing the model in the CAD, the part is optimized for manufacturing and sent to the printer.
While additive manufacturing is capable of working with many materials including metals, ceramics, and even biochemicals, it is primarily associated with the use of thermoplastic because of its ease of use. Because of the use of plastics, the product can be much lighter than metal parts. While the research and development that has gone into improving thermoplastics have been fruitful and productive, 3D printed parts are still behind metal parts in terms of strength, and the production process is limited to short-runs due to the cost. These factors in-tandem means that additive manufacturing is still at its best when applied to one-off parts and prototypes.
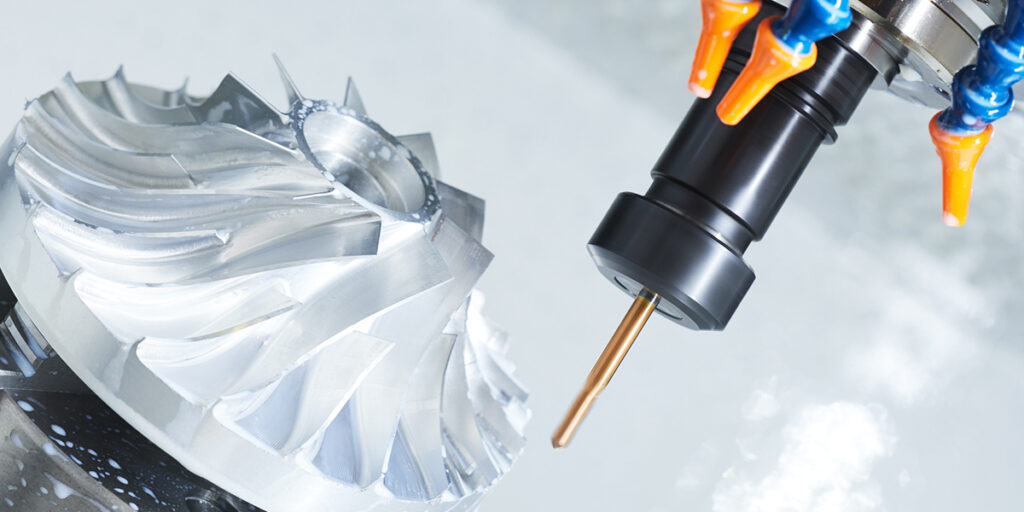
While additive manufacturing is great for prototyping, subtractive manufacturing is ideal for developing the final part.
Subtractive Manufacturing
Subtractive manufacturing is what we often think of when we think of manufacturing. It is the umbrella term for many controlled machining and material removal processes. These processes start with solid blocks or bars of metal or another material, which is shaped by the removal of the material through processes like cutting, boring, grinding, and drilling. While the history of manufacturing and CNC machining dates back centuries, modern CNC machines use G-code, CAD, and computer-aided machining (CAM) to craft and shape the part out of the stock.
Often cited as a disadvantage of subtractive manufacturing, it does take time to program the machine so it knows where and how to cut the workpiece, but once the programming is complete, the machine will continuously and reliably craft precision parts. This makes subtractive manufacturing an ideal choice for long-run production and maintaining a large supply of parts to use in your products at a much more affordable price than additive manufacturing/3D printing currently allows for.
So, when it comes to deciding which manufacturing technique is right for you, it all depends on what you need. If you’re in the research and development stage of production, then additive manufacturing and 3D printing is a great solution, but if you need more parts in a more cost-effective setup, then subtractive machining and the automation CNC machining brings with it is the ideal solution for you.
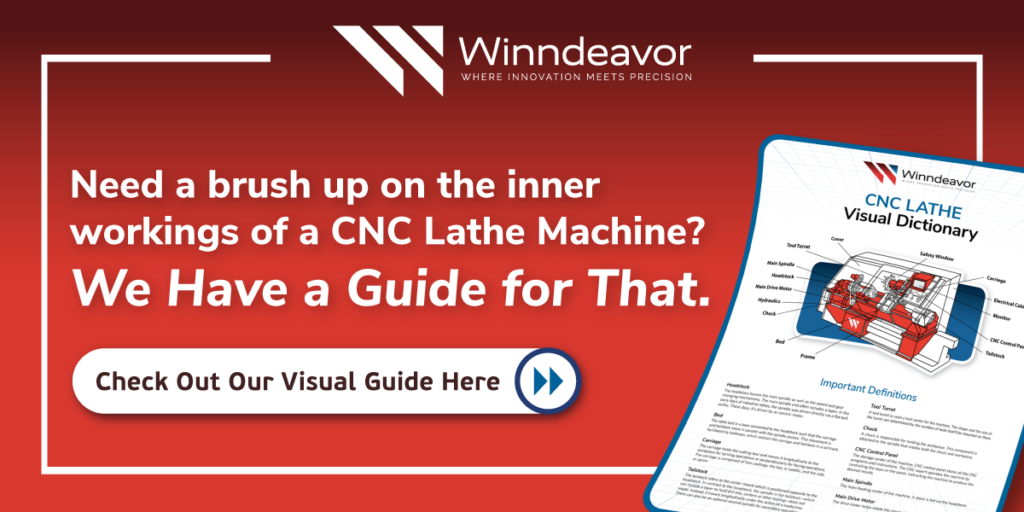