As industries push the envelope of technology, decision-making hinges on the insights drawn from advanced testing methods. Destructive and non-destructive testing serves as the dual foundations of product development, merging the drive for innovation with the imperatives of safety and quality. Join us as we discuss how these testing strategies inform crucial choices in product manufacturing and maintenance.
Stay Ahead of Supply Chain Issues with Our Helpful Infographic!
The Crucial Role of Testing
To begin, we must first understand why testing is important. Testing in manufacturing ensuring that every component of an item meets rigorous standards of safety, performance, and durability before the final product reaches the consumer. By testing different attributes such as tolerance levels, manufacturers gain valuable data that helps streamline production and supports further improvements. Advantages of testing include:
- Quality Assurance: Testing verifies products are built to last and perform as expected under various conditions, which is critical for maintaining brand reputation and consumer trust.
- Regulatory Compliance: Many industries are governed by strict regulatory standards that require rigorous testing.
- Risk Reduction: By identifying potential failures and material deficiencies early, testing mitigates risks associated with product failures in the market. This can lead to recalls, legal issues, and financial loss.
Destructive and Non-Destructive Testing: What’s the Difference?
Both destructive and non-destructive testing are tools used to provide a comprehensive overview of a product’s health and capabilities. So, what makes each unique?
Destructive Testing
The objective behind Destructive Testing (DT) is straightforward: push a material or product to its limits to understand its threshold. In doing so, you can confirm if a product meets stringent safety and quality standards. Methods of destructive testing include:
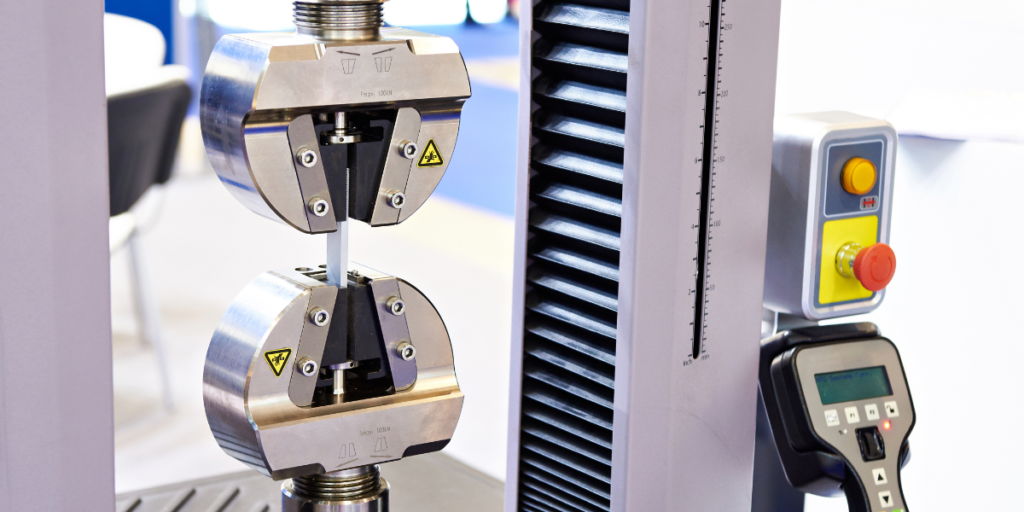
Destructive testing methods such as tensile testing can help find the limits of a products capabilities.
- Tensile Testing: Measures tensile strength, yield strength, and ductility by elongating a specimen until it fractures, revealing how materials behave under tension.
- Hardness Testing: Assesses resistance to indentation using methods like Rockwell, Brinell, and Vickers, which involve measuring the depth or size of an indentation made by a hard indenter.
- Fatigue Testing: Evaluates a material’s durability under repeated loading and unloading to determine its longevity and failure point under cyclic stress.
- Compression Testing: Analyzes material behavior under compressive loads, measuring its ability to withstand squeezing forces and its deformation characteristics.
- Impact Testing: Determines material toughness by measuring the energy absorbed before fracture when struck by a hammer or pendulum, simulating high-rate loading conditions.
- Shear Testing: Tests the material’s ability to resist sliding forces by applying a parallel force to its surface, evaluating shear modulus and shear strain.
- Flexural Testing (Bend Testing): Investigates how materials behave under bending stress through simple beam loading, crucial for components that bear loads.
- Fracture Toughness Testing: Quantifies resistance to brittle fracture in materials with pre-existing cracks by measuring their capacity to withstand crack growth under stress.
- Creep Testing: Measures a material’s deformation resistance under a constant long-term load, especially at high temperatures, providing insights into its time-dependent deformation rate.
Non-Destructive Testing
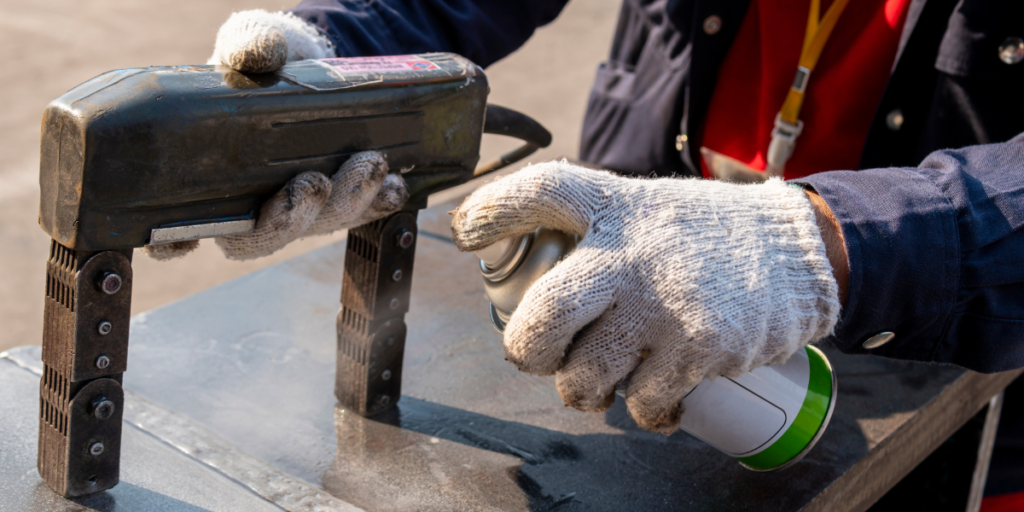
Non-destructive testing methods such as magnetic particle inspection find potential issues without causing damage.
Non-destructive testing (NDT) is all about precision and conservation. Technicians use NDT to detect flaws or anomalies without impacting the component’s ability to be used afterword. Here are a few examples of non-destructive testing methods:
- Ultrasonic Testing (UT): Employs high-frequency sound waves to detect internal defects or characterize materials.
- Radiographic Testing (RT or X-ray Testing): Uses X-rays or gamma rays to view the internal structure of a component.
- Magnetic Particle Inspection (MPI): Detects surface and near-surface discontinuities in ferrous materials.
- Liquid Penetrant Inspection (LPI): Reveals surface-breaking defects by bleed-out of a colored or fluorescent dye from the flaw.
- Eddy Current Testing (ECT): Uses electromagnetic induction to detect surface and near-surface flaws in conductive materials.
- Visual Inspection (VI): This simple NDT method involves looking at a component to spot surface defects.
- Acoustic Emission Testing (AET): Detects transient elastic waves generated by the sudden redistribution of stress in a material.
- Thermography (Infrared Testing): Uses infrared imaging and thermal cameras to detect sub-surface defects through variations in thermal emissions.
- Leak Testing (LT): Includes several methods (like bubble testing, pressure change, and halogen diode detection) to identify and locate leaks in a system.
- Ground Penetrating Radar (GPR): Employs radar pulses to image the subsurface and is used in concrete inspection, among other applications.
Choosing Between Destruction and Preservation
Different industries have different stakes in product reliability and safety. Industries such as aerospace, automotive, and construction might lean towards NDT because it allows them to test products and materials in real-time without rendering them unusable. For example, Minot Air Force Base uses non-destructive inspection to guarantee their 5th Bomb Wing’s fleet of B-52H Stratofortress lack defects. On the other hand, industries that produce single-use items or that need to test to the point of failure might prefer DT methods.
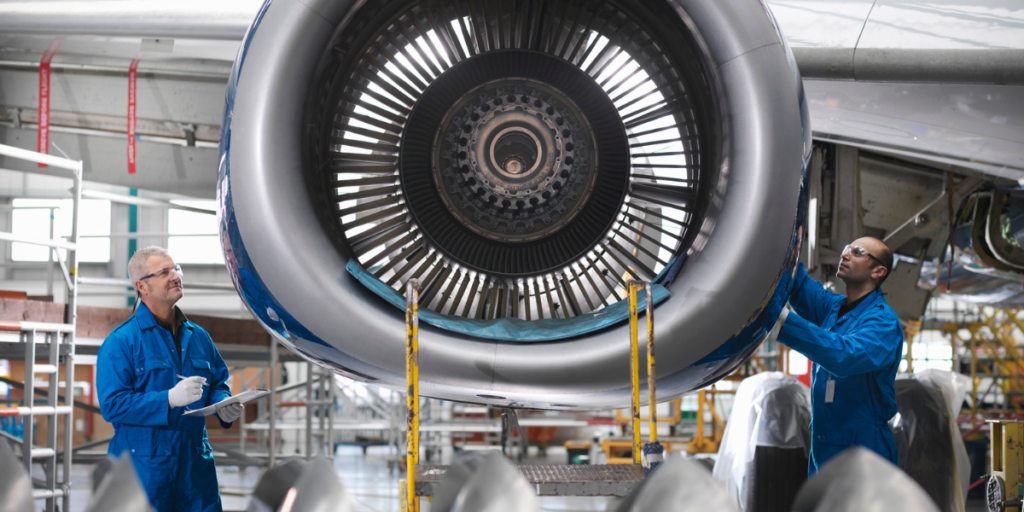
Both destructive and non-destructive testing offer valuable insights across different industries.
When it comes to selecting the appropriate testing method for you, several factors come into play:
- Project Budget: DT can be more costly in the long run since it destroys test samples, while NDT, although potentially higher in initial costs, preserves the integrity of materials.
- Safety Requirements: Industries where safety is non-negotiable, such as aviation and automotive, cannot compromise on the integrity of their materials, making NDT a necessity.
- Product Lifecycle: For single-use items or prototypes, destructive testing might be the practical choice. Conversely, for products with longer lifecycles, non-destructive testing could be more advantageous.
Find Success with Destructive and Non-Destructive Testing
The decision to use destructive and non-destructive testing is a strategic choice that affects every step of a product’s development from conception to market. Making an informed choice is vital for both the success of your product and the integrity of your manufacturing process.
At Winndeavor, we understand the complexities of this decision-making process. Let this guide serve as a starting point for identifying the best testing protocol for your needs. And when in doubt, remember that our expertise is just a consultation away.
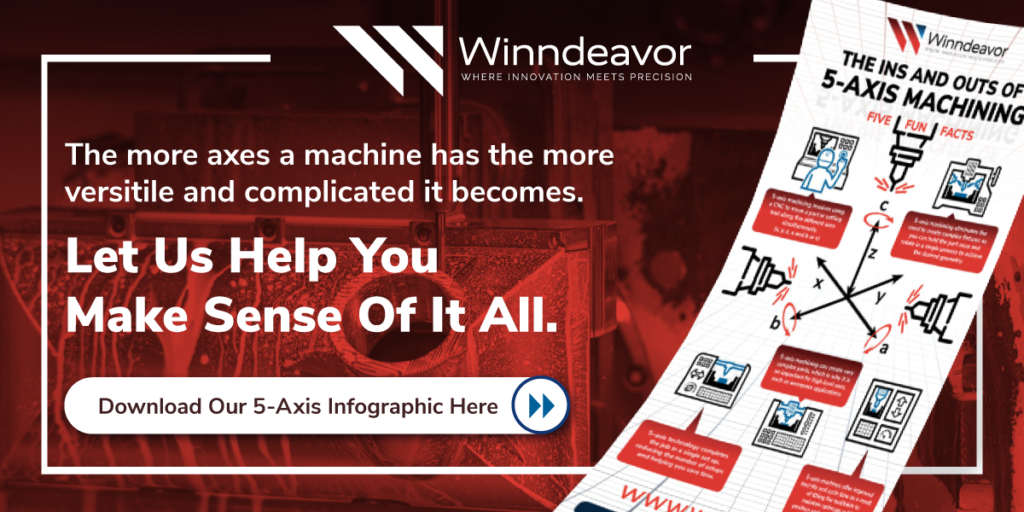