If you rely on the expertise of a precision machining company, you may have come across the term “Production Part Approval Process” or PPAP. But what does it mean; and, more importantly, why should you care? In this blog post, we delve into the basics of the Production Part Approval Process and its benefits in today’s manufacturing world.
Streamline Inventory Management – Download Your Comprehensive VMI Checklist!
What is the Production Part Approval Process?
The Production Part Approval Process is a series of steps used to identify and mitigate manufacturing problems, ensuring suppliers meet their customers’ requirements for product quality. It is a collaborative effort between the supplier and the customer, emphasizing transparency, communication, and accountability throughout the production process.
Originally developed for the automotive industry, PPAP has since gained widespread adoption across multiple manufacturing sectors, including aerospace and medical part production. It serves as a standardized method to verify all necessary engineering design records and processes have been properly documented and validated. This means fewer turnbacks and revisions, which is beneficial in every industry.
Basic Steps of the Production Part Approval Process
PPAP consists of several key elements that need to be completed and documented. While the amount of steps within the Production Part Approval Process vary depending on the manufacturing industry and its guidelines, some of the basics are as follows:
Design Records: Including dimensional drawings, engineering specifications, and any other relevant design specifications that outlines the product requirements
Engineering Change Documents: Any updates made to the design records during the manufacturing process must be documented and communicated.
Process Flow Diagram: A detailed diagram illustrating the step-by-step process of producing the part.
Control Plan: A list of inspections required to control and verify the product’s quality at each stage of the manufacturing process.
Measurement System Analysis (MSA): A measurement study conducted to ensure the inspection methods and instruments used are reliable and accurate.
Part Submission Warrant (PSW): A document signed by the supplier confirming all the necessary requirements specified in the PPAP have been met.
When manufacturers diligently complete these elements and follow the Production Part Approval Process, they gain the trust and confidence of their customers, ensuring consistent quality, timely delivery, and adherence to specifications.
The Benefits of PPAP
By implementing the Production Part Approval Process, manufacturers:
1. Establish a Clear and Traceable Documentation Process
PPAP requires suppliers to document and validate all engineering design records, procedures, and process flows. This documentation provides a comprehensive record of the entire production process, making it easier to identify and correct any issues.
2. Identify and Address Potential Risks
Through the Production Part Approval Process, both suppliers and customers have an opportunity to identify and address any potential risks that may affect product quality or delivery. Because of this, any issues are resolved before impacting the final product.
3. Streamline Communication and Collaboration
PPAP encourages open communication and collaboration between suppliers and customers. This fosters a more transparent relationship, leading to increased trust and a stronger partnership between both parties.
Take the Next Step
As a precision machining company, Winndeavor understands the importance of delivering high-quality products. We take our quality control process seriously so that our customers receive results that meet their exact specifications every time. Contact our team today to learn more about our services and how we can assist you with your machining needs.
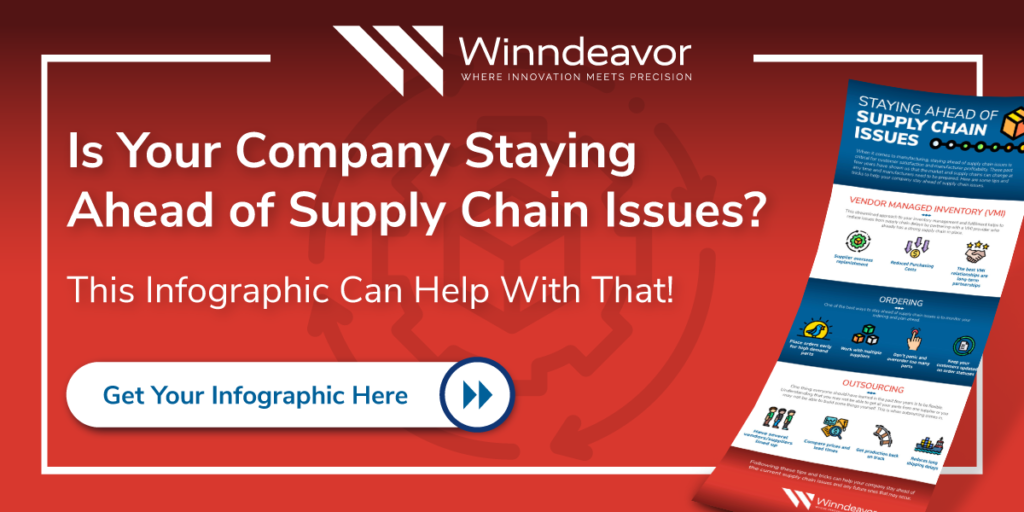