Broaching is one of the most common machining processes. It’s used to removed selected material from a workpiece to create specific and unique features. How does broaching differ from other machining processes though? And when should you use broaching tools over other tools to get the job done? There are many reasons why broaching tools make a difference in the manufacturing process, which is why we want to show you what broaching tools are used for and how they can help you and your machining process.
Learn the Ins and Outs of 5-Axis Machining
What is a Broaching Tool?
A broaching tool (or just broach) is a cutting tool used to cut a specific shape or remove a specific area from the workpiece, many times on the internal diameter of a workpiece. The broach is commonly used in a lathe or attached to a machine powered by hydraulic pressure. The broach is then pushed or pulled through the workpiece, removing material with each pass to create specific features and shapes.
Types of Broaching Tools
Choosing the right broaching tools for your shop’s needs can help speed up production times and increase precision in the final product. There are many types of broaching tools to choose from, each with their own special use:
- Square broach
- External broach
- Internal broach
- Diametric broach
- Internal helical groove broach
- Single or double keyway broach
- Rectangular broach
- Internal gear broach
- Rotary broach
With broaching, you also have the option of push or pull broaching. Push is often used with low speed and high compression, while pull is optimal for high-volume work and can be used horizontally or vertically.
What Are They Good For?
Broaching can also be used to cut more complicated shapes that cannot be achieved with other tools. Some of the shapes possible with broaching are:
- Hexagons
- Keyholes
- Squares
- Odd, irregular shapes
- Unconventional cuts inside of materials
Broaching can be used by many different types of industries. Some of the most common are:
- Automotive parts
- Fasteners
- Firearm components
- Industrial manufacturing
By using broaching tools, manufacturers can cut precise shapes into the material that would often be more complicated or impossible with other machinery. Broaching tools can combine the three stages of required machining that you would typically see in other tools. Rough, semi-finish, and finish cutting can all be done using a broach. This is possible because a broach is made up of several levels of cutting teeth. Since broaching tools can finish all three steps in rapid succession, broaching is popular for bulk precision machining.
Broaching Tools Require Care and Maintenance
While there are many benefits to broaching, there is one key point to consider. Broaching tools and machines require regular maintenance to keep them running at their best teeth on the tools can easily be damaged or worn down if not properly care for with regular maintenance.
It’s easy to see that broaching tools can make the machining process more precise and efficient by creating unique, unconventional features quickly and easily. But a broach isn’t a one-size-fits-all solution. Take time to consider if broaching tools are a good fit for the part you are trying to make. Visit our website today to learn more about broaching and other types of machining. We are always happy to help!
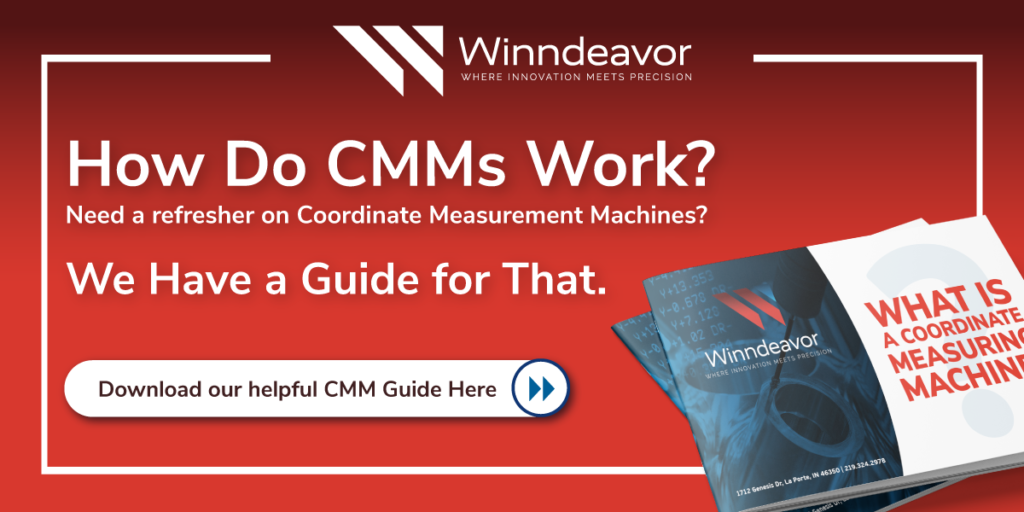