When it comes to manufacturing, few processes are more versatile than CNC machining. CNC—short for computer numerical control—is a method of automating machining work through a computer. In subtractive CNC machining, a piece of metal is shaped and cut to meet the specified demands programmed into the computer allowing the part to be crafted with high levels of precision without an operator or supervisor, removing human error from the machining process.
Click Here to Learn About Setting Up Vendor-Managed Inventory
It probably comes as no surprise, but computer-guided machining is a noticeable improvement over non-computerized machining. But where did computer numerical control come from? Innovation and technology has sure come a long way in just under 300 years, so let’s discuss a brief history of CNC.
Where better to begin than the beginning? James Watt and Matthew Boulton had built steam engines in in the 1760s and ’70s, but they needed to use hammered iron, which caused leakage past the piston. That is, until 1775 when John Wilkinson invented what is widely considered the first machine tool: a boring machine which held the cutting tool on both ends and extended through the cylinder. This produced cylinders with a 50-inch diameter, allowing Boulton and Watt’s steam engine to run more efficiently—powering the Industrial Revolution.
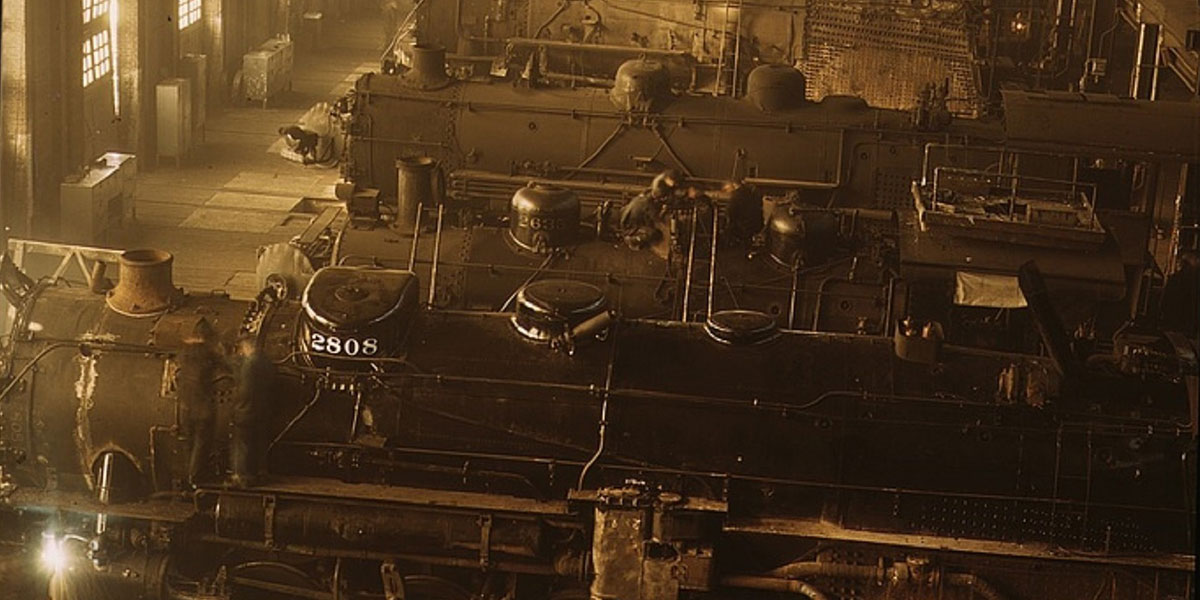
In 1775, John Wilkinson created what is widely considered the first machine tool, which in turn helped to create a more efficient steam engine.
Now, let’s jump back a little bit. In 1725 France, Basile Bouchon invented a way to control textile looms using data encoded on paper through punched holes. Though groundbreaking, the method still required an operator until 1805 when Joseph Jacquard used sturdier cards in a sequence to automate the process, though a worker needed to “code” the cards: punching holes in them by hand. In essence, the loom “read” the cards to “select” threads and allow hooks to pass through on a yes/no basis–binary code.
Punched cards would find their usefulness in various applications throughout the 1800s including telegraphs and self-playing pianos. Herman Hollerith used them for electromechanics and in 1896, he founded the Tabulating Machine Company, which we now call IBM.
So, at this point we have machines and we have computers, so now we need to put them together. This leads to servomechanisms, which were created by H. Calendar in England in 1896. A servo is an automatic device that corrects the performance of machines or mechanisms. A servomechanism is made up of a device being controlled, another which gives commands, and an error detector, and an error corrector. In CNC machining, servos are vital for achieving required tolerances.
Even though servomechanisms were available, it would still be nearly 50 years before they reached their application in aerospace. In 1942, pioneer John Parsons started using numerical control (NC) to craft helicopter rotor blades; he perfected the process in 1946 when he hired engineer Frank Stulen. Stulen had the idea of using IBM’s punch cards—they were still manually punched!—to better determine how much stress the rotor blades could handle. Shortly after, 1949, the US Air Force employs Parsons to construct precise plane wings.
The next evolution of would arrive in 1956 when MIT would develop the Automatically Programmed Tool (APT), a language created to work with MIT’s Numerical Control (NC) machine. The leader of the project, Douglass Ross, would later create the term “computer-aided design,” which we now call CAD, though it would be Patrick Hanratty, a computer scientist at GE who would earn the title “Father of CAD” for writing the Pronto language in 1957 which later CAD programs would use.
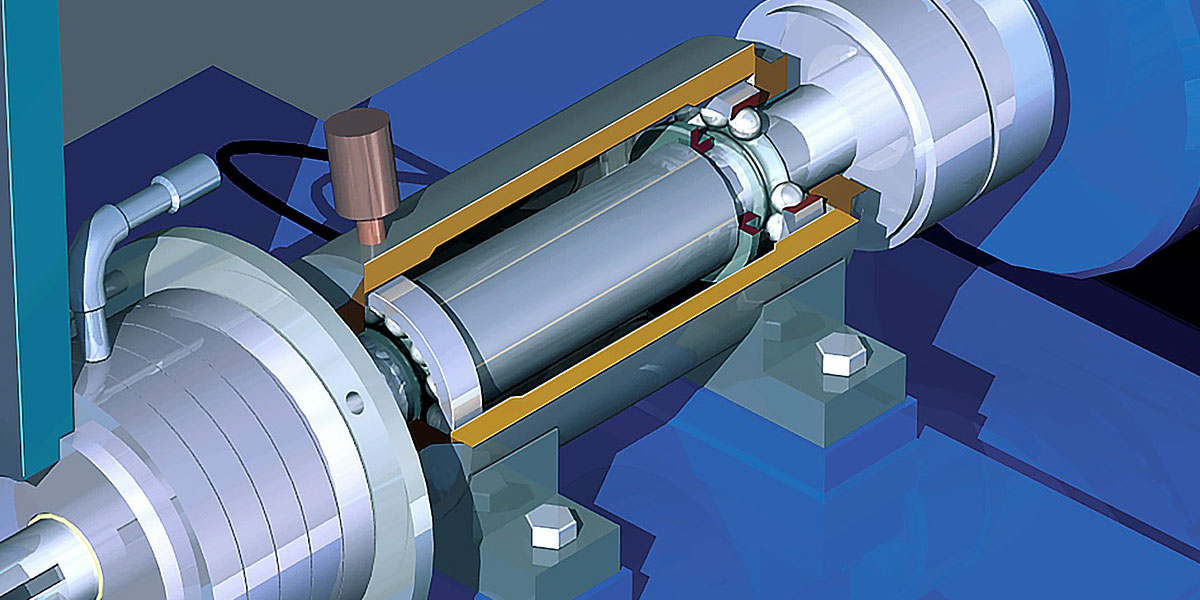
Through the use of CAD software engineers can design complex parts and send the information directly to a CNC machine for production.
In the sixties, computers started to get smaller and computers and NC came together to finally create CNC. With slow economic growth in the seventies, CNC became a cost-effective solution and its usefulness only increased as personal computers like the Apple II and Macintosh put computing power into the hands of everyday people and, importantly for us, machinists.
Today, CNC continues to push the limits of machining. Gone are the days where equipment can only do one job. Where once equipment could only mill or turn, we now have machines that perform multiple tasks and work in up to six axes (future technology will make that statement will look antiquated one day).