When the last Ice Age carved the Great Lakes and a mighty system of rivers in what would become “the American Midwest,” the groundwork was laid for a manufacturing powerhouse to build upon. Millions of years later, this system of rivers would provide transportation for travelers, but mills and dams would also harness the power of water to build the infrastructure we all rely on today.
Learn the Ins and Outs of 5-Axis Machining
It is often thought that the presence of manufacturing infrastructure was a key factor in the North winning the Civil War: they were able to build and replace damaged guns and cannons far quicker than their Confederate opponents, but even after the War, in places like Pittsburgh and Detroit, the presence and power rivers provided allowed industrialists like Andrew Carnegie and Henry Ford to build their respective business empires in the late 1800s and early 1900s. Cities like Pittsburgh, Detroit, Chicago, Toledo, Buffalo, and Milwaukee would grow into metropolitan manufacturing hubs for customers all over the world. While the future was looking bright, trouble was on the horizon.
Beginning in the 1960s and 70s, Midwestern cities across states like Pennsylvania, Ohio, Indiana, Michigan, Illinois, and Wisconsin became known as the Rust Belt. During this timeframe, these states experienced economic and population downturns as many businesses sought out the warmer clients of the American south, known as the Sun Belt, or abroad. Literally, the factories were left behind to rust—hence the region’s nickname. Between 2000 and 2018, Detroit’s population had decreased by over 29%, Gary, Indiana’s had dropped 26.7%, and Cleveland’s fell just under 20%.
Cities like Detroit would become known for low jobs numbers and high levels of poverty; the heartbeat of America’s automotive industry was fading. Foreign cars from Japan and other countries became dominant on American streets: these cars were smaller, more fuel-efficient, and cheaper than their American counterparts. This would be particularly damaging from October 1973 to March 1974, when the Organization of Arab Petroleum Exporting Countries placed an oil embargo on the US and allies, resulting in a dramatic surge of fuel prices.
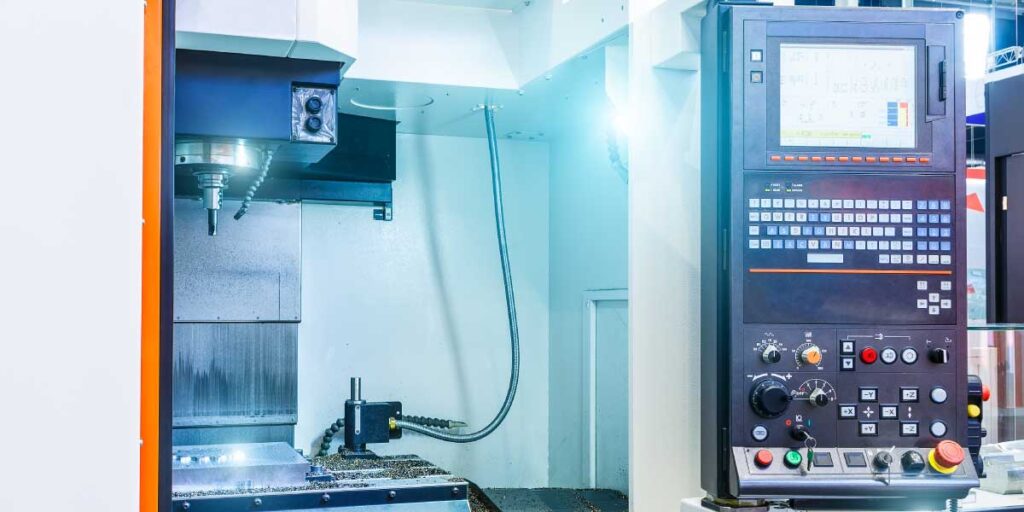
Midwest manufacturers have always embraced new innovations in machine technology and tools.
For a Northern Indiana connection, in 1965, South Bend-based Studebaker attempted partnerships with both Nissan and Toyota that would see Japanese cars rebadged as Studebakers: such was Studebaker’s desperation. The story goes, though, that Toyota was insulted at being Studebaker’s second choice and Nissan was unhappy Studebaker representatives were talking to Toyota in the first place, so no partnership occurred, and Studebaker would shut down within two years.
Workers who relied on the automotive industry to feed their families began to lose their jobs, culminating with Chrysler, GM, and even the city of Detroit itself filing for bankruptcy. By 2008, the Federal Government was bailing out the automakers and in 2014, what was left of Chrysler was sold to Italian automotive manufacturers Fiat. Dark times had set in on the region.
So, what does the future hold for manufacturers in the Rust Belt? Well, new types of research and development in some nontraditional manufacturing techniques and methods have emerged in recent years that are at the heart of the region’s revitalization. The increased usage of robots and automated systems make machine shops more efficient and productive, allowing them to better meet client needs and in a faster timeframe.
For manufacturers in the Rust Belt, we know the value of being nimble and agile in an unpredictable world. Whether you just call it the Midwest or the Rust Belt, manufacturers in this region have always been ready to face the next challenge. It’s simply in our blood. We always work toward new innovations to improve our services and our processes.
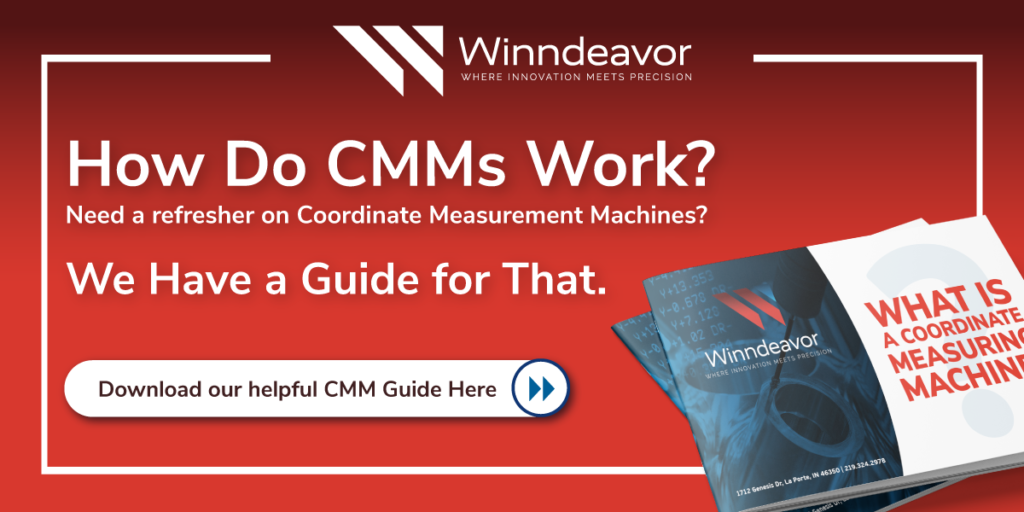