Whether the work is for original equipment manufacturers (OEMs), aftermarket product companies, or racing teams, improved machining techniques and technologies, coupled with computer numerical control (CNC) have continuously helped to push automotive machining. As shops continue to pursue more effective measures for process and quality control, data-driven strategies have been adopted. How have advancements in CNC helped propel automotive machining? Let’s find out.
Click Here to Download Our Guide to CNC Lathes
Machining technologies have been improved and have enabled automotive parts to be manufactured more effectively. Five-axis machining, in particular, has found its application in crafting automotive parts like cylinders and combustion chambers. The latter specifically requires complex, contoured geometry as well as a high-quality surface finishes that are perfect for five-axis CNC machines. Tool-changing machines are also great for crafting automotive parts because they make the need to transfer the part from one machine to another obsolete. Instead the part can stay at the same station while the machine itself changes its cutting head, making CNC machining a highly efficient, time-saving, profit-maximizing solution for creating auto parts.
Professional racing engine builders, specialize and thrive on getting maximum power and performance out of their engines. They do this through a combination of precision engineering and optimizing the combination of parts. This requires either modifying mass-produced parts or creating customized ones. Now, modified off-the-shelf components may improve performance slightly, but when the goal is optimal performance pushing the limits of vehicles, only custom parts will do. This is exactly why CNC machining is needed to make our engines better than before.
For us who don’t drive supercars, CNC machining is doing good for us, too. Programming the machine to craft something like an engine block may be a time-consuming process requiring a specialized skill set, but once the program is done, the machine carries it out without human assistance, so productivity increases without a significant increase in labor.
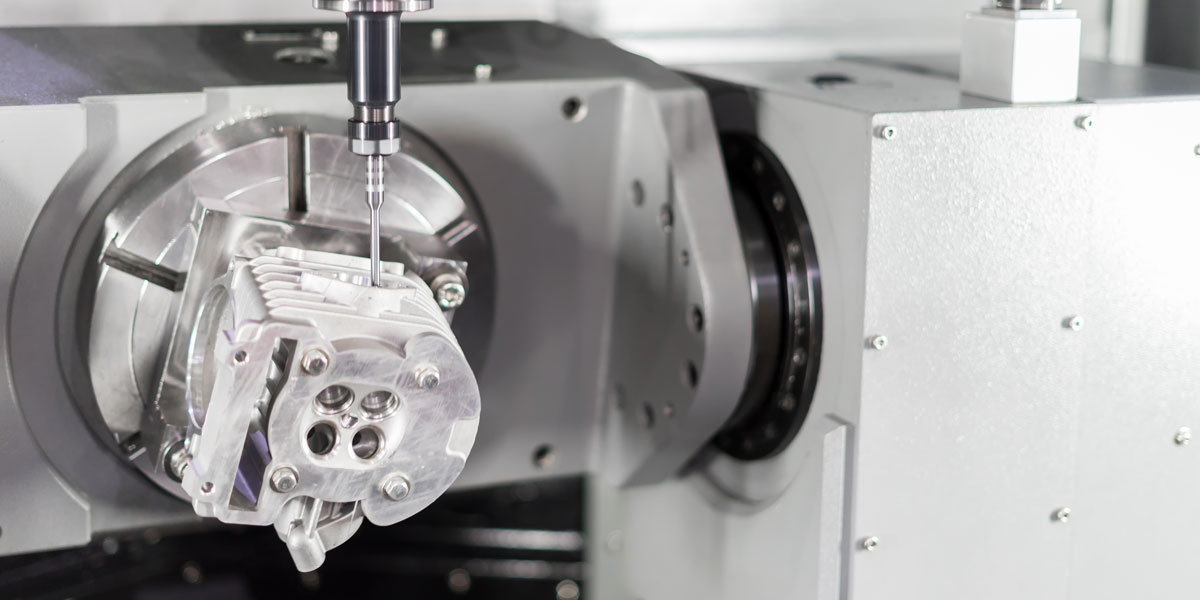
A five-axis machine milling a combustion chamber.
CNC has many advantages in the automotive industry. First, its varied utility. In addition to engines, it is also used to craft headlights, exhaust parts, fluid system components, bushings, carburetor housings, powertrains, and valve retainers. Second, CNC machining provides speed to manufacturers, which is particularly evident when a large volume is being made because while people get fatigued, the computer is tireless. Next, CNC is highly accurate, providing precision and tight tolerance: eliminating human error. Finally, the same CNC program can be repeated without deviation between parts, which is particularly useful in an industry like automotive in which demand is high.
As we have seen in this study of automotive machining, CNC is shaping both the present and future for the metalworking industry. For your metalworking needs, the team at Winn Machine is committed to getting the job done. We look forward to partnering with you.