Orthopedic manufacturing is a demanding industry that involves difficult to work with materials, complex geometry, and litigious quality standards. But with the right materials and precision machining processes, an experienced machine shop can successfully produce medical-grade parts with efficiency and quality.
Keep Your Supply Chain Running Smoothly – Download Our Helpful Infographic!
Common Materials Used in Orthopedic Manufacturing
Just like any industry that requires manufactured parts, the choice of material for component production is a conscious decision. The material must meet the specific criteria the part will undergo when in use. For orthopedic components, materials are chosen based on strength, rigidity, resistance to corrosion, and biocompatibility. A joint implant that breaks easily simply won’t do.
A commonly used material in orthopedic manufacturing and across medical manufacturing in general is medical grade titanium. The strongest grade of titanium with the highest corrosion resistance, medical grade titanium is highly favored for its compatibility with the human body. Other materials used for orthopedic manufacturing include:
- 316 stainless steel
- 17-4 stainless steel
- Anodized high-strength aluminum
- Polyvinyl chloride—or PVC
- Polyether ether ketone—or PEEK
- Polyoxymethylene—also known as POM or acetal
Orthopedic Precision Machining Processes
Equally as important as the materials used for orthopedic manufacturing are the precision machining tools used to build the component. With increasingly complex parts needed within the industry, machine shops must meet the demand with processes that are repeatable and precise, allowing for dimensional controls at even the most minute of scales.
One such solution is computer numerical control—or CNC—machines. Designed for high-precision results, CNC machines have improved process controls and automation. This contributes to its repeatability and reliable production yield. Swiss turning, in particular, is a type of CNC lathe that can produce items smaller than 0.75” in diameter. This is in part because the part can be machined with hard turning, which allows for turning along intricate contours and crafting micrometer sized features.
Another crucial component to orthopedic manufacturing is the need for five-axis machining. Saving on production time by eliminating the need to move complex parts to different machines, components can be manufactured in a single location with a high degree of accuracy. Five-axis machines also achieve superior surface finishes compared to other machines—which is particularly important in the orthopedics industry where a smoother surface minimizes the risk of infections.
Winndeavor: The Quality Choice for Precision Machining
Orthopedic manufacturing requires efficiency, accuracy, and quality. With a commitment towards quality, Winndeavor is equipped with the tools described above as well as other precision machining instruments to successfully achieve your goals. Contact Winndeavor today and experience the best in orthopedic manufacturing.
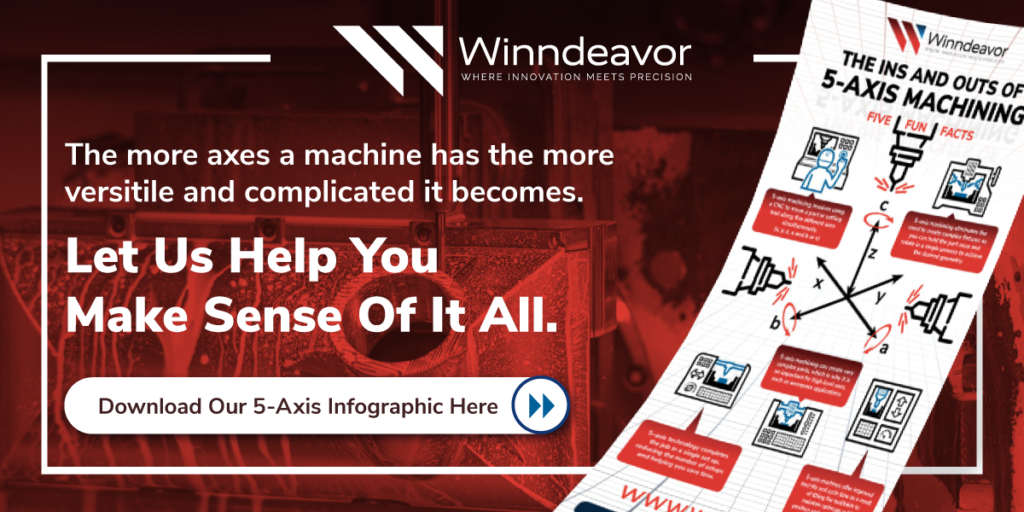