Thanks to Swiss turning, machining high volumes of small, extremely detailed parts has never been easier. How and why did a technique invented in the 19th century for Swiss watchmaking become an essential part of modern shop floors? Let’s find out.
Learn the Ins and Outs of 5-Axis Machining
What is Swiss Turning?
Swiss turning refers to the use of a Swiss-style lathes to make parts. Unlike other conventional turning machines, the Swiss-style lathe utilizes a sliding headstock—hence why they’re also referred to as sliding headstock machines. This feeds bar stock though a guide bushing along the Z-axis, out through the spindle, and past the stationary cutting tool. This means the point of contact for the cutting tool is always near the bushing, which allows for greater support and reduced vibration and tool deflection. With greater tolerance comes greater ability to produce smaller size and more detailed parts with a reduced risk of production errors.
3 Benefits of Swiss Turning
When you can manufacture intricate parts on a smaller scale, there’s a trickledown effect of advantages across your entire operation. Because of Swiss turning, you can:
Say Goodbye to Small Part Problems
Where a conventional turning machine might struggle to work on small, long, and slender objects, Swiss lathes excel. Swiss turning can produce items less than 0.75” in diameter. Its high tolerance threshold even allows for hard turning, which can be important for detail-oriented work on micrometer sized features. Along with the parts being less difficult to produce, the chance of operator errors and the wasted money, time, and materials associated also decreases.
Double Productivity
Because the likelihood of errors is higher, conventional turning methods require longer production cycles. Swiss turning cuts the cycle in half: yielding more results in less time. Additionally, many Swiss lathes include sub-spindles so multiple operations can be done simultaneously. Combined with the fact that they usually have double or even triple the number of axes compared to other CNC lathes, it may not even be necessary to use another machine to complete the process. This can also reduce the labor cost associated with using multiple machines.
Maximize the Work Zone
Being able to isolate production down to a single instrument frees up other machines, so you can optimize operations. Because more machines are now available, shops can take on more work and leave the larger projects to those machines. Thus, there’s an opportunity to not only produce more, but to also have a larger variety of items in production.
Take the Complexity Out of Small Parts
Swiss turning can make an amazing difference in producing the intricate parts required for industries spanning from aerospace to healthcare and everything in between. So, the next time you need small, highly detailed parts in large batches, make sure you look for a partner with the Swiss advantage.
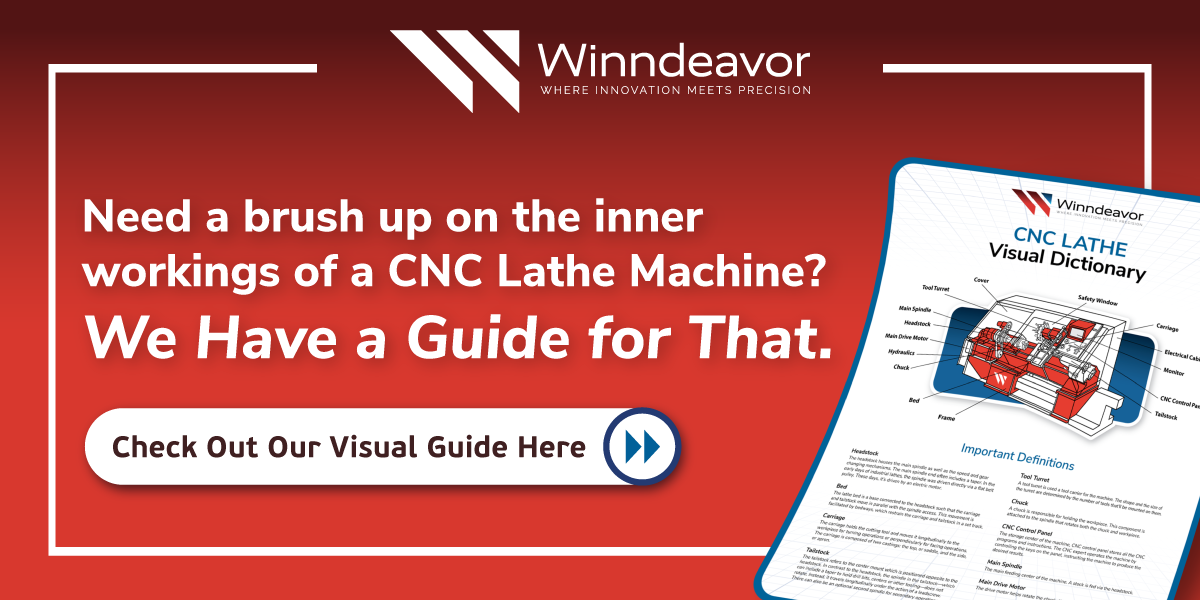