When it comes to machining parts, precision is key. However, even the most skilled machinists run into trouble when a part is damaged or flawed. That’s where non-destructive testing (NDT) comes in. NDT is a set of techniques used to identify defects and flaws in a material without causing damage to the tested part. How does this work? A couple of different ways. Join us as we discuss the world of non-destructive testing and some of the common methods used to ensure part quality.
Streamline Inventory Management – Download Your Comprehensive VMI Checklist!
What is Non-Destructive Testing?
Non-Destructive Testing (NDT) is a testing technique that identifies defects or flaws in materials without causing any damage to the tested parts. Some forms of NDT are possible even if a part has complex geometries that would be difficult or impossible to inspect using visual methods. This makes it a valuable technique for manufacturers who want to ensure that their parts meet the necessary standards without causing any further issues. NDT is particularly useful in industries such as the aerospace, automotive, and medical industries—where defects have potentially catastrophic consequences.
In Comparison to Destructive Testing Methods
NDT provides significant advantages compared to traditional destructive testing methods. For one, NDT is often more cost-effective than destructive testing, since it doesn’t damage the tested parts. This results in significant material savings, particularly in industries where high-value materials are used. Additionally, NDT allows manufacturers to retain the integrity of the tested part, which is important for those in critical applications.
6 Different Methods of Non-Destructive Testing
There are several different methods of NDT, each suited to different types of applications in the machining industry.
Visual Testing (VT): This deceptively simple technique involves meticulously examining the surface of a part for issues such as cracks, corrosion, scratches, dents, and other forms of surface damage. VT is a non-intrusive, cost-effective method that can be readily incorporated into the inspection process and is usually an initial step before applying more advanced NDT methods.
Ultrasonic Testing (UT): This method uses high-frequency sound waves to examine the internal structure of a material. UT is particularly useful for detecting defects in welds and for testing the thickness of a material.
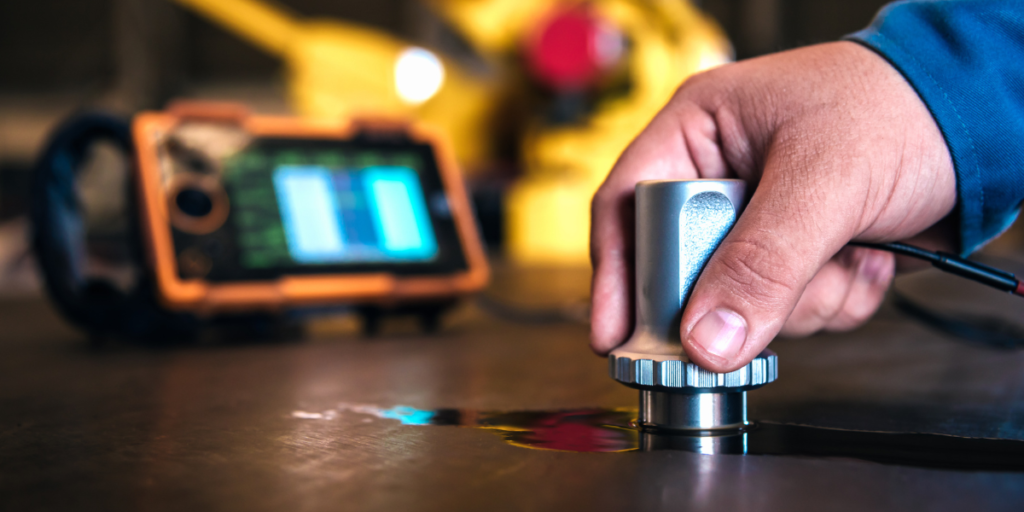
Ultrasonic testing is valuable because the high frequency sound waves can detect defects that are invisible to the naked eye.
Magnetic Particle Inspection (MPI): MPI employs magnetic fields to detect defects in ferrous materials. It is particularly useful for detecting surface flaws, and for testing parts that are highly stress loaded.
Liquid Penetrant Testing (LPT): LPT is a technique for detecting surface cracks and other surface defects using a dye or fluorescent penetrant. It is useful for testing parts that are exposed to corrosive materials.
Radiographic Testing (RT): RT uses X-rays or gamma rays to inspect the internal structure of a material. This is particularly useful for testing the thickness and density of a material.
Eddy Current Testing (ECT): Using magnetic fields, ECT detects changes in electrical conductivity in a material. It is useful for detecting surface cracks and defects in metals, and for testing conductive coatings.
Learn More About Quality Assurance with Winndeavor
In the machining industry, non-destructive testing is a vital tool for testing and validating parts’ quality without causing any damage. If you’re interested in learning more about quality assurance in manufacturing, Winndeavor is a valuable resource for industry insight and expertise.
Our dedicated team of experts has created insightful blogs about the Six Steps of the Quality Control Process and the Production Part Approval Process, providing invaluable resources for improving your manufacturing processes and meeting your goals.
Don’t settle for second-best in your industry; partner with Winndeavor today to take your quality assurance practices to the next level. Get in touch with a member of our talented team to learn more!
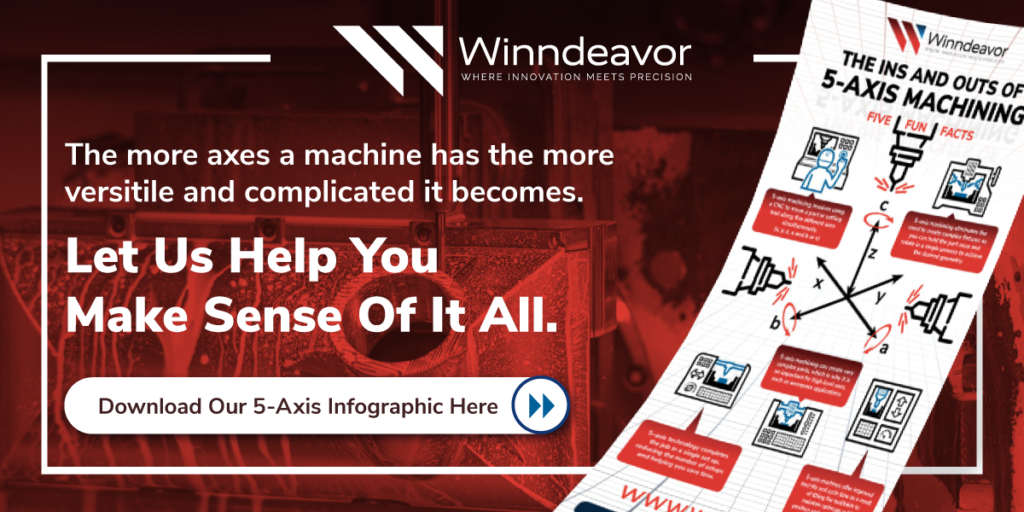