Precision is key when it comes to manufacturing and machining, especially when working with complex shapes. Like many materials, some metals are easier to work with than others, making the precision machining process more difficult. There is one process, though, that is well known for its ability to accurately machine complicated shapes and materials. This process is known as electrical discharge machining.
Learn the Ins and Outs of 5-Axis Machining
What is Electrical Discharge Machining?
Electrical discharge machining (EDM)—sometimes known as spark machining and arc machining—is a process used to precisely cut/shape difficult materials. This is achieved using electrical currents passed through an electrode and a workpiece/material. The electrode and material are separated by a dielectric liquid, which acts as an insulator until enough voltage is applied to reach its ionization point, at which point, it becomes a conductor. The spark discharge that comes from this erodes the material until the desired final shape is created. Because electrical discharge is an important part of the EDM process, any material must be electrically conductive for the process to work.
History of EDM
The process behind modern EDM has been around for decades, and the basic principles have been noted for centuries. The knowledge that electrical discharges can have erosive effects was first studied by physicist Joseph Priestley in 1770.
The process behind die sinker EDMs is traced back to two different groups working independently of each other in the 1940s. Both groups were looking for solutions to other problems when they discovered the possibility of using electricity to erode metals. The history of wire EDM is lesser-known, but we do know that it was developed throughout the 1960s and 1970s.
Types of Electrical Discharge Machining
The types of EDM are typically grouped into three categories:
- Die Sinker or “Ram” EDM
- Electrodes that are custom made into 3D shapes produce a cavity in the material that is the imprint of the electrode.
- Wire or “Cheese Cutter” EDM
- This type of EDM uses a thin wire to cut the material.
- Hole Drilling or “Hole Popper” EDM
- Similar to die sinkers, this form uses a cylinder to machine a hole into the material.
What is Dielectric Fluid?
Dielectric fluid is not one specific type of fluid, but rather refers to any fluid that can be used in the EDM process. Different types of EDMs may use different types of dielectric fluid. Die sinker EDM machines will typically use hydrocarbon oil, while wire EDM machines normally use deionized water. There are three main functions for dielectric fluids:
- Keeping the spacing of the sparking gap between the electrode and material under control
- Cooling the heated materials
- Removing the EDM chips from the sparking areas
Electrical discharge machining allows for precision when cutting difficult materials and complex shapes. Decades of research and trials have led to the EDM process we now have today, which is only getting better as technology continues to grow and evolve. EDM is great for those looking for a predictable, accurate, and repeatable process. If you have questions about these machining processes, contact our team today!
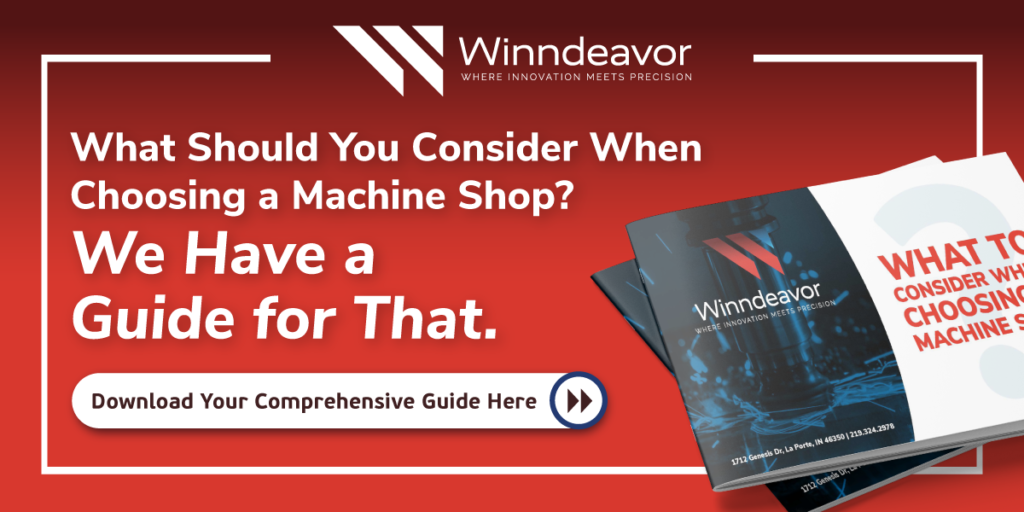